-
Speed of Installation
Starting with product design, our data centre façades are engineered for maximum installation efficiency. Key design features include optimised installation sequences,
reduced fixing and component parts, and simplified sub-structures, all of which significantly speed up the installation process.The overall façade design also plays a crucial role in the installation efficiency as systematic and regular patterns can effectively reduce installation time. While the precise installation method varies between façade products, our in-house pre-construction team are experts in data centre façades and collaborate early in the process to maximise success.
-
Buildability
By engaging with architects at the early pre-construction stage, we gain a deep understanding of the design intent of the façade and actively contribute to it. Buildability is a key concept where we ensure that the façade’s design principles align with manufacturing processes, while optimising installation
methods. This approach not only influences the façade’s design but also has commercial benefits, such as minimising material waste and carefully planning the installation process for maximum efficiency. -
Modern Methods of Construction
Modern Methods of Construction (MMC) are offsite techniques designed to accelerate construction, reduce costs, eliminate waste, and maintain high quality. These methods include offsite assembly and product design, as well as finite element analysis (F.E.A.), which tests design principles and concepts
in the early stages.The benefits of MMC are significant, including reduced material usage, minimised components, and decreased manual handling. For data centre façades, these techniques offer vast potential for cost efficiency, material savings, waste reduction,
improved health and safety, and environmental benefits.
CAPABILITIES
Maple Façades is a leader in architectural façade systems, specialising in data centres. Our unique Proven Process guides projects from inception to completion, ensuring they are buildable, manufacturable, and safely installed on time and within budget.
INSTALLATION EFFICIENCY
-
ISO Accreditations
Health and safety is at the heart of the Maple business and our processes and policies are documented in great detail. We are consistently audited through UKAS Management System procedures and certified with zero non-conformances in the following ISO accreditations:
ISO-9001 (Quality Management) provides a framework for businesses which helps to improve performance, meet client expectations, and display a commitment to quality.ISO-14001 (Environment Management System) assures both internal and external stakeholders of the organisation that environmental impact is being considered and measured.
ISO-45001 (Health and Safety) reduces the amount of workplace injuries, illnesses, and incidents by enabling businesses to systematically assess hazards and implement risk control measures.
-
Safety - No Riddors or LTI's for over 5 Years
RIDDORs are reportable incidents resulting in seven or more days of absence from work and LTI’s are any period of absence from work due to an accident.
-
Sustainability
In addition to upholding excellent health and safety standards, we are committed to minimising the environmental impact of our activities. The first Life Cycle Assessments of our products in 2023 led to independently verified Environmental Product Declaration documents, marking a significant step towards our goal of achieving Net Zero by 2026.
EXCEPTIONAL
HSEQ
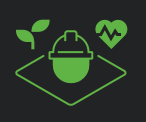
-
Onsite QA Checks
Maple’s onsite teams are fully equipped with the latest technology and training to carry out comprehensive assessments and surveys. Our procedures include detailed passive fire reporting, weekly site reports, and thorough inspection and test plans for all Maple-installed products, ensuring that all processes run smoothly and efficiently on site.
-
Pre-construction & Design
At Maple, we like to get under the skin of a project long before we arrive on site. Our pre-construction team provides design proposals at RIBA stage two or three, exploring value engineering options through 3D technologies. Utilising finite element analysis, sampling, mock-ups, and pre-construction design, we ensure your project is commercially buildable. Our design team uses modern software and technologies, including Autodesk Inventor, Revit, and support for BIM modelling, to provide comprehensive support.
-
Production Facility
Our in-house production and storage facilities in our factory HQ in Stockport remain at the forefront of the façade industry. The factory spans 18,000 square feet across three areas with designated assembly bays and cutting areas. Our external yard and stillages also offer storage space for vested materials.
PROJECT EXECUTION PLANNING
“From tender to contract, into design and
installation at the site, Maple have been one of
the easiest subcontractors to deal with.”